Что мешает использовать инновационные технологии обработки металла на российских предприятиях
О том, что от экспорта сырья и полуфабрикатов России нужно переходить к выпуску продукции более высоких переделов, говорят давно, но в нынешней ситуации это жизненно необходимо. Мнением о том, что мешает развитию современных производств, с "РГ" поделился генеральный директор Регионального центра лазерных технологий (РЦЛТ) Анатолий Сухов.
Анатолий Георгиевич, вы начали заниматься внедрением лазерных технологий обработки металла и, по сути, их пропагандой более четверти века назад, когда о промышленных лазерах в России еще мало кто слышал. Ставка на фотонику себя оправдала?
Анатолий Сухов: Наше предприятие было зарегистрировано 13 июня 1997 года как Региональный центр листообработки. На старте было непросто: чтобы приобрести первые станки, мы выиграли гранты, в том числе участвовали в международной программе с ФРГ. Но все получилось, и с тех пор предприятие развивается, наращивает парк оборудования и компетенции. И я по-прежнему убежден, что лазерные технологии дают огромное преимущество, существенно расширяют возможности металлообработки, в первую очередь благодаря высокой скорости и точности.
Но сегодня установки для лазерной резки и сварки уже имеются на многих заводах, в том числе на Урале. Конкуренция серьезная?
Анатолий Сухов: В этом я не вижу для нас проблемы, по крайней мере, пока: заказов у РЦЛТ достаточно. Наши преимущества - это и огромный опыт, и широкий набор производимых операций. Я бы даже сказал, что название - центр лазерных технологий - нам уже немного мешает. Сегодня РЦЛТ может выполнять практически любые виды металлообработки, не только лазерную резку, сварку, нанесение упрочняющих покрытий, но и традиционные операции: гибку, фрезерование, обычную аргонодуговую сварку, вальцовку и т. д. Для этого мы купили десятки современных станков и обрабатывающих центров.
На форуме "Армия-2023" РЦЛТ организует конференцию "Инновационные технологии и материалы для ОПК. Развитие кооперационных связей"
Такой набор оборудования многократно расширяет возможности предприятия. Например, выполняем крупные и сложные заказы для крупнейших машиностроительных компаний региона: для Уральского турбинного завода изготавливаем подшипниковые узлы, цилиндры низкого и среднего давления, для Уралмашзавода делаем взамен импортных профилированные настилы, а также кузова экскаваторов, в том числе в арктическом исполнении (из морозоустойчивых марок стали). Кроме того, впервые поставили кабину для экскаватора "ИЗ-КАРТЭКС" - полностью укомплектованную, вплоть до кондиционера и микроволновки для комфорта оператора. Это был первый такой опыт для нас, но не последний: получили аналогичные заказы.
Наше преимущество - комплексный подход, сочетающий изготовление образцов, отработка инновационной технологии, создание 3D-модели, изготовление эффективной оснастки, производство изделия, контрольная сборка и, наконец, серийное производство. Это позволяет снизить себестоимость изделия в некоторых случаях на 30 процентов. Отмечу: помимо стальных мы делаем самые разные конструкции из алюминия, нержавейки, титана - эти металлы весьма капризны, мало кто умеет с ними работать.
Титан используют не только авиастроительные корпорации?
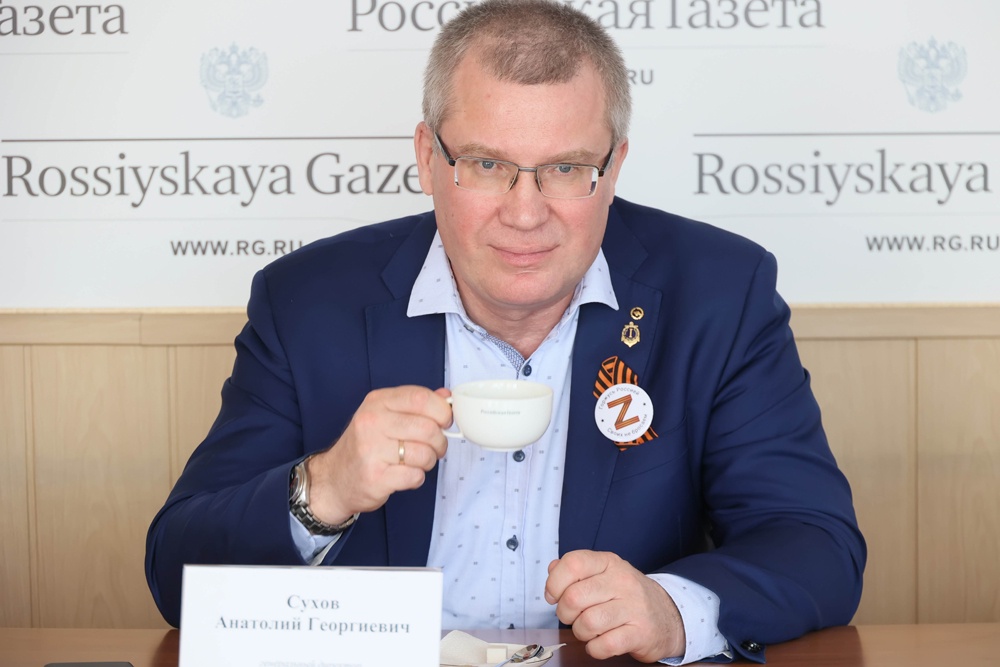
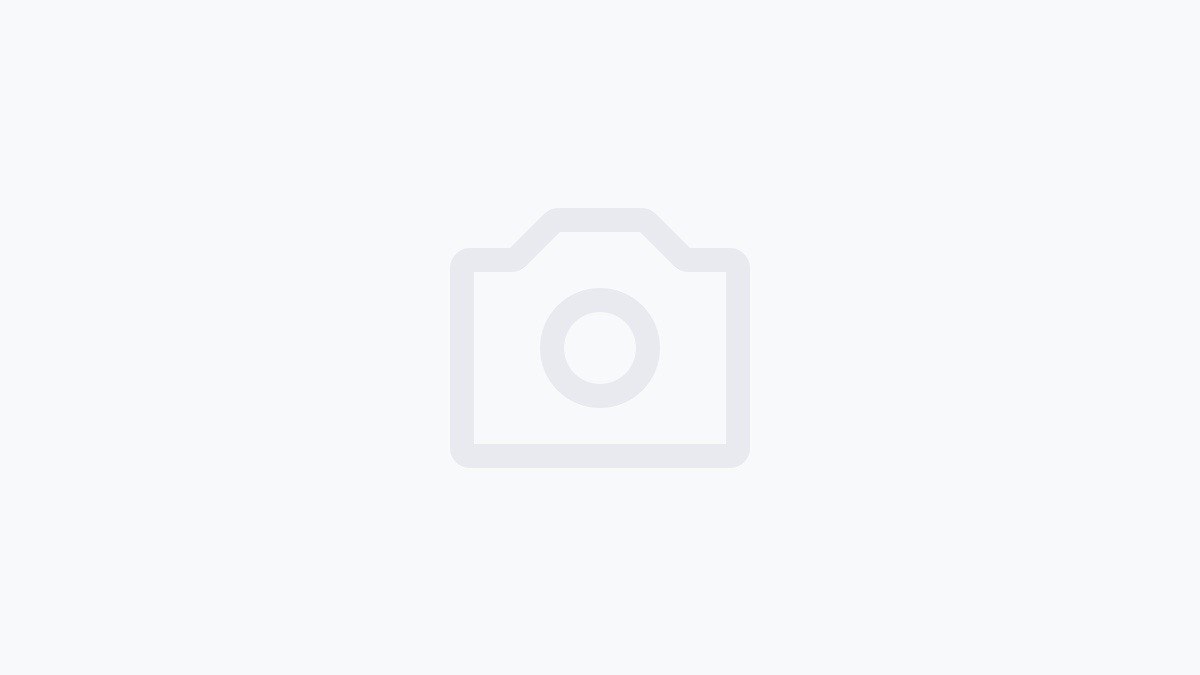
Анатолий Сухов: Конечно, нет! Благодаря своей прочности и легкости этот металл имеет огромные перспективы. Например, РЦЛТ изготовил из титана опытную партию деталей для аппаратов Илизарова для Центрального института травматологии и ортопедии - они гораздо легче обычных. Если изделие успешно пройдет испытания, то будет использоваться для лечения детей.
Есть и более масштабный пример - металлоконструкция для радиолокационной системы (РЛС) корабля. Серийно РЛС изготавливается из нержавеющей стали, титановая вдвое легче - это потребовалось при модернизации судна, чтобы снизить нагрузку на мачту. Задача нетривиальная, и выполнить ее нужно было в очень короткий срок. Мы проработали технологию, создали специальную оснастку. Самые большие сложности возникли на этапе монтажа конструкции: все процессы нагрева-остывания должны происходить в среде защитных газов, по сути, в вакуумной камере. С относительно небольшими узлами вопрос решается просто, а вот со сборкой пришлось повозиться. Чтобы было понятно: это конструкция массой 600 килограммов и высотой более 3,5 метра, она состоит из 260 с лишним деталей. Буквально на днях натуральный образец вернулся с испытаний. Уверен: новое изделие пойдет в серию. Это была интересная задача, решение которой существенно продвинуло нас самих.
В этом году вы уже не в первый раз будете участвовать в международном военно-техническом форуме "Армия" в Кубинке. Что планируете показать?
Анатолий Сухов: В прошлом году у нас был стенд площадью 24 квадратных метра, в этом планируем 40. Безусловно, представим там титановую конструкцию РЛС. А еще покажем макет ордена "Победа", который администрация Екатеринбурга попросила нас сделать к 300-летию города. Это металлическая многослойная конструкция диаметром около 3,5 метра, она будет установлена на проспекте Космонавтов взамен прежней.
Но главное - мы организуем на форуме "Армия-2023" конференцию "Инновационные технологии и материалы для ОПК. Развитие кооперационных связей". Ее участники - представители научных институтов, профильных кафедр российских вузов, крупных промышленных предприятий. Планируем поднять отраслевые проблемы и обсудить пути их решения. В частности, с докладом о развитии производства титанового проката выступит глава ассоциации "Титан" Андрей Александров.
С этим есть проблемы? Удивительно, ведь у нас, в Свердловской области, работает ВСМПО-АВИСМА - крупнейший производитель титана в мире.
Анатолий Сухов: Это в советские годы у нас производили до 100 тысяч тонн титана в слитках, тогда как весь остальной мир - 25 тысяч. (Замечу: все 100 тысяч шли на внутренний рынок, ведь титан - это стратегический материал.) В последние годы ВСМПО дает 30 тысяч тонн, из них до недавнего времени внутри страны потреблялась треть, а две трети забирали "Боинг", "Эйрбас" и другие мировые корпорации. Для сравнения: Китай сегодня производит 165 тысяч тонн слитков.
В России есть определенный дефицит титанового листа. Дело в том, что везде в мире его катают на тех же станах, что и нержавейку, и себестоимость получается в несколько раз ниже, чем у нас. Чтобы удовлетворить потребность внутреннего рынка, а она превышает 12 тысяч тонн, нужно решить эту проблему. Например, Трубная металлургическая компания запускает новый прокатный стан в Волгоградской области на 100 тысяч тонн - под сварную нержавеющую трубу. Если бы они начали катать на нем еще и титан, это способствовало бы укреплению нашего технологического суверенитета. Не нужно соперничать с Китаем, но необходимо отстаивать свои национальные интересы, обеспечивать внутренние нужды. Необходимо расширить сотрудничество предприятий, производящих и обрабатывающих этот металл.
Кроме того, есть проблема и с сырьем, при том что Россия занимает четвертое место в мире по его запасам. В СССР титановую губку производили в основном на Украине, в Казахстане, а в России - в Березниках. Сейчас есть дефицит сырья, поэтому необходимо комплексное освоение новых месторождений внутри страны, и это государственная задача.
Что еще мешает развивать в России металлообработку, чтобы производить высокотехнологичную продукцию?
Анатолий Сухов: Не секрет, что современное оборудование практически все импортное, в том числе и у нас в РЦЛТ. Мы успели существенно пополнить свой парк до санкций, но последний станок ждали уже больше года - с его получением возникли серьезные сложности. Так же, как и с запчастями для имеющегося оборудования, с программным обеспечением. Пока мы эти вопросы решаем, в том числе с помощью собственной сервисной службы, но риск сохраняется. И это системная проблема, которая актуальна не только для нас.
Однако есть и еще более острая - кадровый голод. Мы готовы за счет компании обучать целевиков, начиная с колледжа и до магистратуры. Но сложно даже набрать желающих. Найти готовых специалистов на рынке труда тоже практически невозможно: конкуренция по зарплатам сейчас жесточайшая.
Но мы не опускаем руки, активно сотрудничаем с учреждениями СПО и вузами. Например, с колледжем имени Ползунова с 2021 года проводим форумы по новым технологиям, принимаем студентов на практику. По соглашению с правительством и предприятиями Свердловской области на базе РЦЛТ создан учебно-производственный центр Екатеринбургского политехникума, где с 2013 года обучают рабочих по специальностям в области лазерных технологий. С 2015-го работает на предприятии и базовая кафедра УрФУ, с нашим участием ведется подготовка бакалавров по программе "Лазерные, аддитивные и упрочняющие технологии в машиностроении".
Кстати
РЦЛТ получил грамоту от командования Центрального военного округа за помощь и содействие. На предприятии разработали и безвозмездно изготовили партию деталей спецприменения, произвели ремонт специального оборудования, а также сварили и отправили в войска металлические печки для бойцов.